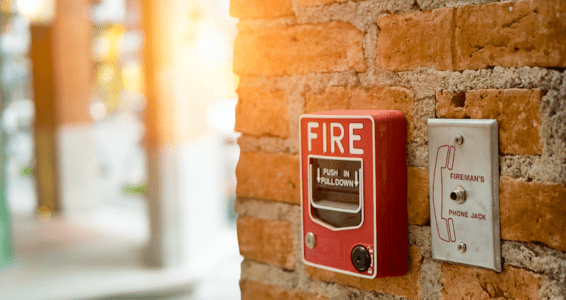
10.20.20 – Facility Executive – By Richard J. Roux, MSFPE, SET, FAI, FAM
When properly designed, installed, inspected, tested, and maintained, fire alarm systems and detectors normally provide many years of fault-free operation.
Today, more than ever, facility managers have a lot on their plate. Managing a large facility with day to day activities is both an ongoing and encompassing job. With a lot of attention, communication and a good staff, business continuity is for the most part, predictable. And yet, there are always those events that just seem to pop up and happen — unforeseen circumstances, like a VIP visit, a failed air handler, or a false fire alarm activation. In spite of these hiccups, the facility management staff can typically deal with them.
Given that many fire protection systems are connected these days, facility managers are increasingly able to react and assess changing situations rapidly. For instance, alarm systems continuously monitor areas within the facility for smoke, heat, flame, carbon monoxide, gas, and other agents. They evaluate the environment and report conditions to the fire alarm control unit which then determines what to do and how to report the condition to building occupants and emergency services.
Alarm systems rapidly detect and evaluate dangerous conditions; this level of continuous diligence saves lives and helps to avert thousands, sometimes millions, of dollars in property damage, and loss.
Early response and compartmentalization are key to mitigation. Systems must be designed, installed, inspected, tested, and maintained to ensure optimal performance. Conversely, a system that is not properly designed or installed will be a source of continuous problems and issues. For example, the wrong type of detector in a space or one that is incorrectly installed, will be a source of irritation and inefficiency for many years. And a detector that is not inspected or appropriately serviced will lead to false activations and unnecessary response. These hiccups will be ongoing and costly; they may cause facility managers to lose faith in their alarm systems.
NFPA 72 Addresses Fire Alarms And Signaling
Several National Fire Protection Association (NFPA) codes and standards deal with fire alarms, smoke control, special agent suppression, security, carbon monoxide, gas systems, elevators, active shooter, and many other topics that are relevant to facility management teams. One of particular note is NFPA 72®, National Fire Alarm and Signaling Code®.

NFPA 72 provides information relative to detectors and provides requirements for their proper installation, testing and maintenance. Understandably, facility managers will not know all the nitty gritty details of NFPA 72, but a basic understanding is critical when outsourcing services. When you hire competent, trained, and qualified practitioners to work on your alarm system, they should be well-versed with all the provisions of NFPA 72.
When properly designed, installed, inspected, tested, and maintained, fire alarm systems and detectors normally provide many years of protection and fault-free operation. However, should any of these be ignored, detectors will be sources of false activation. NFPA 72 does not use the term “false alarm”, instead it uses the term unwanted alarms. Unwanted alarms are characterized as malicious alarms, nuisance alarms, unintentional alarms, and unknown alarms. A nuisance alarm is defined as “an unwanted activation of a signaling system or an alarm initiating device in response to a stimulus or condition that is not the result of a potentially hazardous condition.”
Nuisance alarms are caused by a variety of things but in nearly all cases, these can be traced back to improper detector type (the designer selected the wrong type of detector); installation (the detector is installed in the wrong location or wiring is an issue); inspection (lack of inspection); testing (testing does not follow the manufacturer’s or NFPA 72 criteria); and maintenance (lack of proper maintenance and/or none at all).
Systems that years ago were hardwired and required all conductors to be home run by circuit have migrated to multiplex systems with distributed control panels and more recently, addressable systems with detectors with unique addresses that can individually and continuously communicate with the fire alarm control unit. Modern detectors can provide not only individual data for each detector but imbedded in the communication, the detector can provide heartbeat information, trending, environmental status, sensitivity to alarm, etc. Today’s systems take advantage of a variety of detector types that are self-compensating for environmental conditions and even systems where the unique fire alarm wiring is omitted. Some systems can operate over Ethernet. The 2016 edition of NFPA 72 added Class N, which addressed Ethernet infrastructures for alarm and signaling systems, as well as pathway performance and installation criteria.
More recently, the standards for testing and listing of detectors have changed because the dynamics and content of today’s environments have changed. Not only have fuel loads increased but, there has been a shift from natural materials such as woods and cotton to synthetic materials. Increases in other common base materials include PVC wiring, polyester, acrylic, polyolefin, nylon, ABS, adhesives, laminates, polystyrene, etc. Modern furniture is most often comprised of polyurethane foam these days. Although not all occupancies offer cooking locations, cooking continues to be a very common source of nuisance alarms. In the past, NFPA 72 defined specific rules for the installation of smoke detectors in the vicinity of fixed cooking appliances. Essentially, these rules provided specific distance criteria in feet from the cooking source unless the smoke detector was specifically “listed for installation in close proximity to such locations.” However, there was no such listing so no detectors could be listed for this application and therefore “close proximity” was essentially prohibited. However, the “I know what I am doing,” or “something is better than nothing,” or “I am being told that detection must be installed no matter what” mentality has led to detectors being improperly installed (location is improper).
The standards for testing and listing detectors have also changed their testing criteria to include a paper fire, wood fire, flaming polyurethane foam fire, smoldering polyurethane foam fire, and a unique cooking fire. Detectors that were called “photoelectric” or “ionization” will likely become relegated to history and be replaced with newer single or multiple criteria detectors. These detectors will create a shift in our vocabulary, operation, and resistance to false triggers.
Many facilities rely on their staff to perform inspections, testing, and maintenance activities while others contract services from reputable local companies or national accounts. In both cases, these persons must be trained and qualified. Many states require specific licensing. There are also conditions in NFPA 72 where facility staff are not permitted to perform these services.
Roux is senior electrical specialist at National Fire Protection Association (NFPA). He is Secretary to the NFPA 72 Correlating Committee on Signaling Systems for the Protection of Life and Property. He serves as Staff Liaison to several NFPA Technical Committees, including NFPA 72®, National Fire Alarm and Signaling Code®; NFPA 730, Guide for Premises Security; NFPA 731, Standard for the Installation of Electronic Premises Security Systems and NFPA 715, Standard for the Installation of Fuel Gases Detection and Warning Equipment. Roux is licensed in Massachusetts and is NICET Level IV and IMSA Level II certified. He has been editor and reviewer for many book projects and training programs. He is senior editor of the National Fire Alarm and Signaling Code Handbook. He has written numerous articles on fire alarm systems and authored several fire alarm feature columns.
Want to read more about Fire Safety and Facility Management?
Click here for more NFPA-related news.