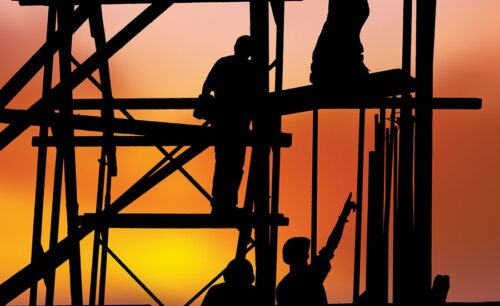
4.17.25 – ISHN- By Rose Morrison
The Occupational Safety and Health Administration (OSHA) guides countless industries in keeping workers healthy and injury-free. Safety managers play a unique intermediary role, communicating these expectations to numerous employees and contractors. Here is how they can design workplace environments to prioritize safety and fight the most frequent safety violations.
The 10 Most Common OSHA Violations
Safety concerns vary by industry, as professionals are exposed to different machinery and environmental influences. These are the most frequently cited standards from OSHA’s fiscal year report across sectors:
- Fall Protection in Construction (29 CFR 1926.501)
- Hazard Communication in General Industry (29 CFR 1910.1200)
- Ladders in Construction (29 CFR 1926.1053)
- Scaffolding in Construction (29 CFR 1926.451)
- Powered Industrial Trucks in General Industry (29 CFR 1910.178)
- Lockout/Tagout, or Control of Hazardous Energy, in General Industry (29 CFR 1910.147)
- Respiratory Protection in General Industry (CFR 1910.134)
- Fall Protection Training in Construction (29 CFR 1926.503)
- Eye and Face Protection in Construction (29 CFR 1926.102)
- Machinery and Machine Guarding in General Industry (29 CFR 1910.212)
Several other prominent concerns include being struck by an object, electrocuted or caught between machinery. Addressing these issues could save hundreds of lives in America and eliminate 21% of deaths attributable to the construction sector.
If safety managers implement measures to tackle the most prevalent threats to worker well-being, they could slash the frequency of the 10 most common workplace injuries.
10 Proactive Steps for Safety Managers
Thoughtful efforts can transform a common safety violation into an infrequent occurrence. Here are several strategies safety leaders can integrate for more comprehensive workplace protections.
1. Use a Comprehensive Safety Management System
These are protocols companies design to organize safety expectations. The procedures identify risks specific to the organization and its sector, personalizing employee recommendations. Usually, guidelines are written or published digitally for easy access.
A guide outlines the organization’s safety goals and metrics and how to achieve them. It should also deliver guidance on what to do in specific emergency or injury-related scenarios, such as how to react and who to contact. Rules on how to report OSHA violations must be available, too. Collect these policies in one place to tackle all the top safety issues simultaneously.
2. Provide Thorough Safety Training
Safety personnel and managers can institute training to adopt new workflows, avoiding predicted risks. Onboarders must receive the same safety orientation and receive regular refresher courses. This includes contractors.
Professionals must maintain logs of all safety education to verify each operator’s knowledge. It can also help provide one-on-one attention if someone is prone to a specific incident type.
3. Establish Regular Inspection Programs
Compliance safety and health officers require regular inspections. Internal safety managers can execute their own as well. Then, they can use the information they gather to prepare for an official OSHA audit.
Workers should be aware of regulatory rules by using standardized checklists that outline how to prep for, interact with and safely exit a jobsite. Track patterns and solve hazards promptly before contacting agencies for review.
4. Create an Effective Hazard Reporting System
If reporting an accident is inconvenient, operators may fail to comply with the procedure. Filing an incident notice must be user-friendly and allow everyone to submit and respond to reports swiftly. Safety managers should have immediate access to them with no delay, especially urgent ones.
Report-tracking software may also help administer corrective action and organize reports by specific employees or incident types.
5. Conduct Regular Job Hazard Analyses
Safety managers can schedule audits to review data on any job hazards and see if particular report types appear frequently. These job hazard analyses process and interpret incident reports and the workplace environment to ensure potential hazards remain low to nonexistent. These analyses can change how the business operates and lead to new projects, such as installing accident prevention through design measures.
During this process, safety experts can document any red flags they notice and update processes accordingly. There are many OSHA violations examples, one being if few supports are available for ladders or contractors frequently ignore them. This observation would be worth noting in a safety report.
6. Maintain Equipment Properly
Countless companies are upgrading equipment, electrifying vehicles and retrofitting with new components. These efforts promise productivity and safety enhancements — if workers know how to use them correctly.
Safety managers must issue preventive maintenance schedules or instruct staff on using tools like sensor-based analytics equipment. Keep records of who last worked on each machine. The information allows teams to identify errors faster during inspections of fail-safes.
7. Use Leading Indicators
Near-miss incidents are as vital to report as accidents and injuries. Near-miss reports can demonstrate other opportunities for improvement while gaining useful insights from the employees on how they avoided safety infractions.
Inform staff of these leading indicators in mandatory meetings to teach them how to adopt hazard correction practices. Regularly review these measures to see if near-miss incidents trend downward, and review employee safety suggestions as needed.
8. Ensure Proper Personal Protective Equipment (PPE) Usage
PPE oversights could lead to almost all of the top 10 most common workplace injuries. Safety managers should provide well-maintained and compliant PPE for all staff. Technicians must be held accountable for helping with their cleaning and maintenance.
They must also report if there are defects, tears or other hazards in the equipment. PPE-specific training helps mend knowledge gaps and instruct users on identifying issues.
9. Develop Emergency Response Plans
Violations involving powered industrial trucks or scaffolding could lead to multiple people getting hurt or a bigger emergency. Staff must know how to identify an emergency, especially when working out in the elements. For example, if a thunderstorm hits the site unexpectedly and causes electrical jolts throughout the property, people must know how to remain safe.
Emergency drills are key to success. These instances should happen infrequently, so the information may gradually fade from the employee’s mind. Safety stakeholders should demonstrate how to use emergency equipment to ensure effectiveness when needed.
10. Foster a Strong Safety Culture
Safety is a culmination of management and employee determination. It is a collaborative effort where all parties hold health and wellness as a value.
This effort also rewards operators who maintain open communication and look out for their colleagues. Information sharing is one of the most crucial factors in a safety culture, so encouraging reports and an environment where employees can voice their concerns will impact performance.
Combating Workplace Injury
By implementing these proactive steps, safety managers can work to prevent the most common OSHA violations and create a safer workplace. Regular monitoring and adjustment of these measures ensures continuous improvement in safety performance.